In many applications strain gauges are utilised in order to measure stress, pressure, force or torque. In propulsion system applications strain gauges are extremely useful as they provide information regarding the torsional stress levels endured by the shaft as well as the bending stresses due to a series of reasons. If strain gauges are arranged at ±45 degrees to the shaft axis, torsional strains and therefore stresses are measured. If strain gauges are arranged in parallel to the shaft axis, bending stresses can be acquired.
Due to the nature of the application a telemetry system is necessary in order to transmit the signals from the rotating shaft to the stationary data acquisition system. Nautilas utilises high quality wireless radio telemetry systems which acquire, amplify, digitise and transmit the signals to a stationary host with the minimum loss of information. The data are thereafter logged and stored on a computer in order to be processed afterwards.
Computational processing of signals can vary from the application of a simple peak-to-peak algorithm to special filtering and Fast Fourier Transform. Information that can be acquired from this process includes:
Performance verification. Propeller torque and power requirements are measured and compared to theoretical predictions.
Torsional vibrations. Identification of the critical speed and the barred speed range of the system. Stress amplitudes due to vibration are measured throughout the operating speed range and compared to classification society regulations.
Verification of engine cylinder balancing. Cylinder-to-cylinder variations are readily visible in the torsional vibration amplitudes.
Verification of propeller dynamic excitation. Levels and frequency of propeller torsional excitation can be measured and compared to predictions.
Shaft alignment verification. Information regarding the alignment condition of the propulsion system. Measuring the variation of bending stresses under static and dynamic conditions, the shape of the shaft and the offsets of the system bearings can be reverse engineered. In this way an assessment of the alignment condition can be made without the need for the shaft to be disassembled.
Information regarding the straightness and concentricity of the shaft journals with respect to the flanges. Bending stresses are measured and analysed in the frequency spectrum. The order and amplitude of the prevailing vibration can therefore indicate problems in the straightness of the shaft.
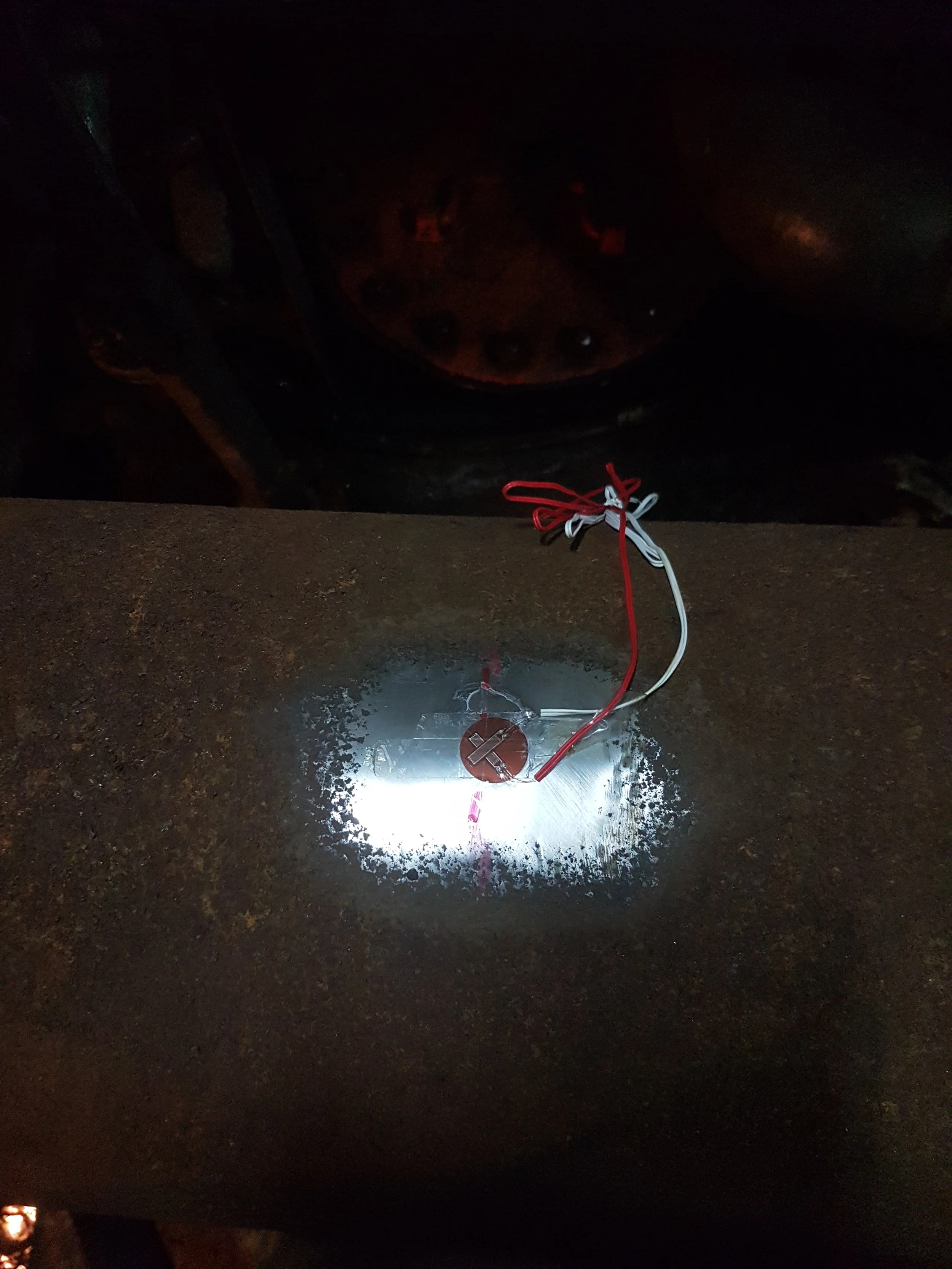



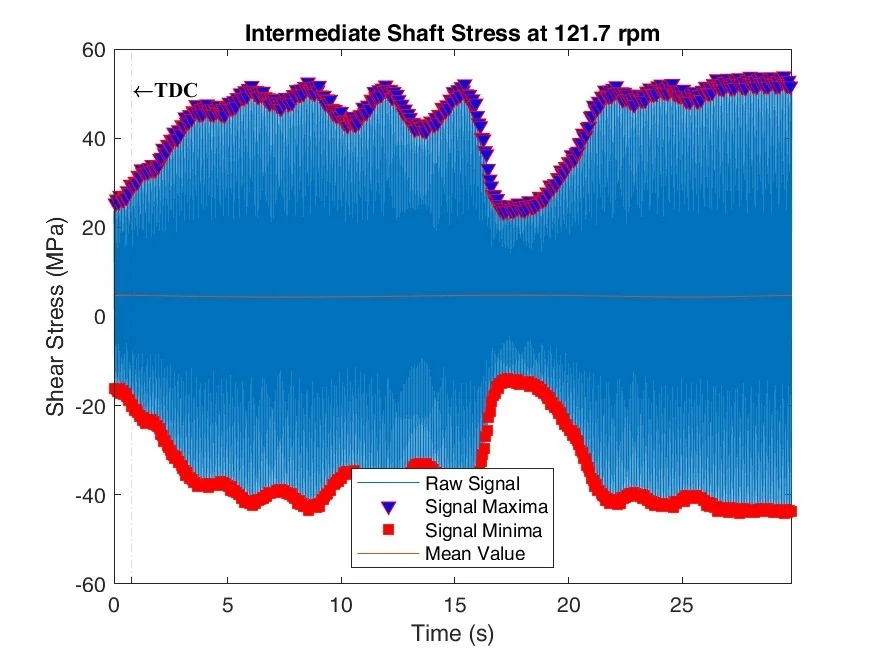

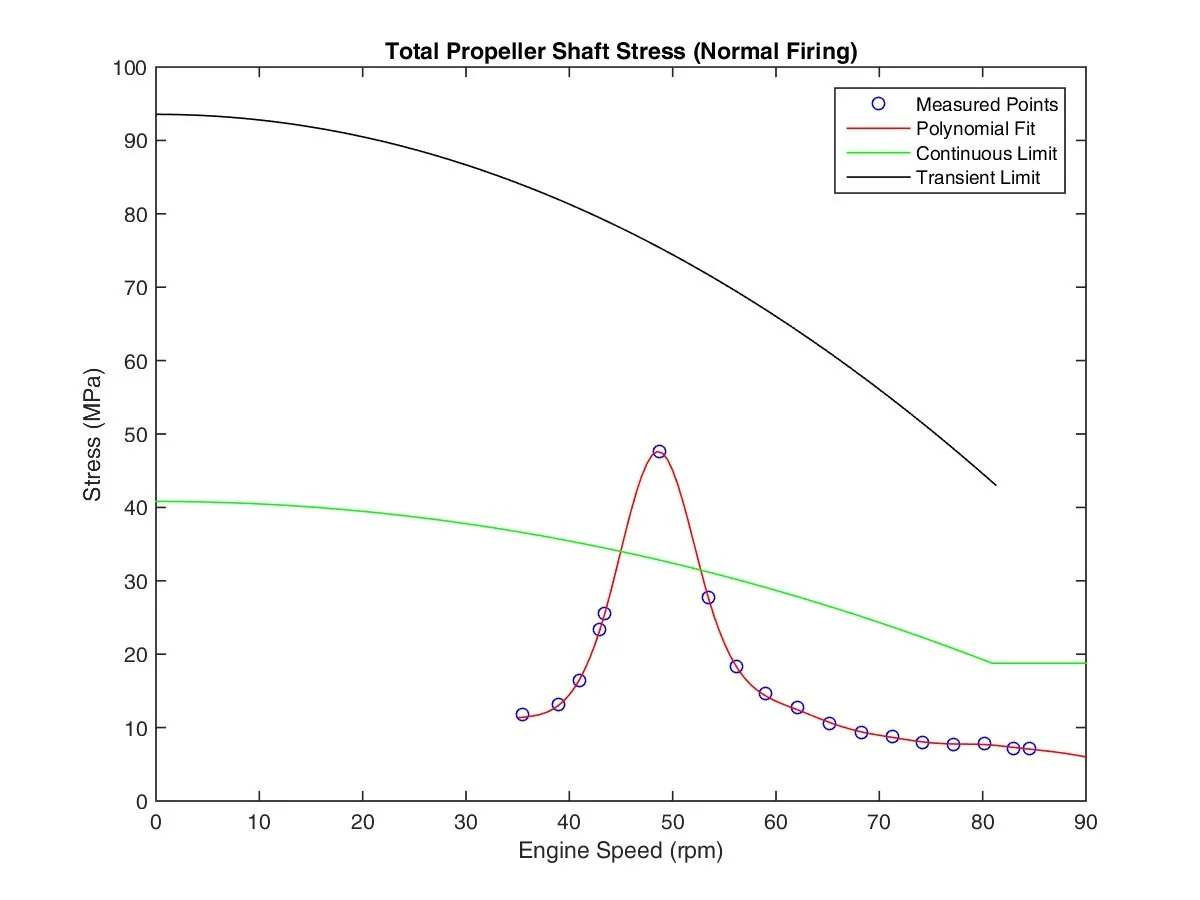

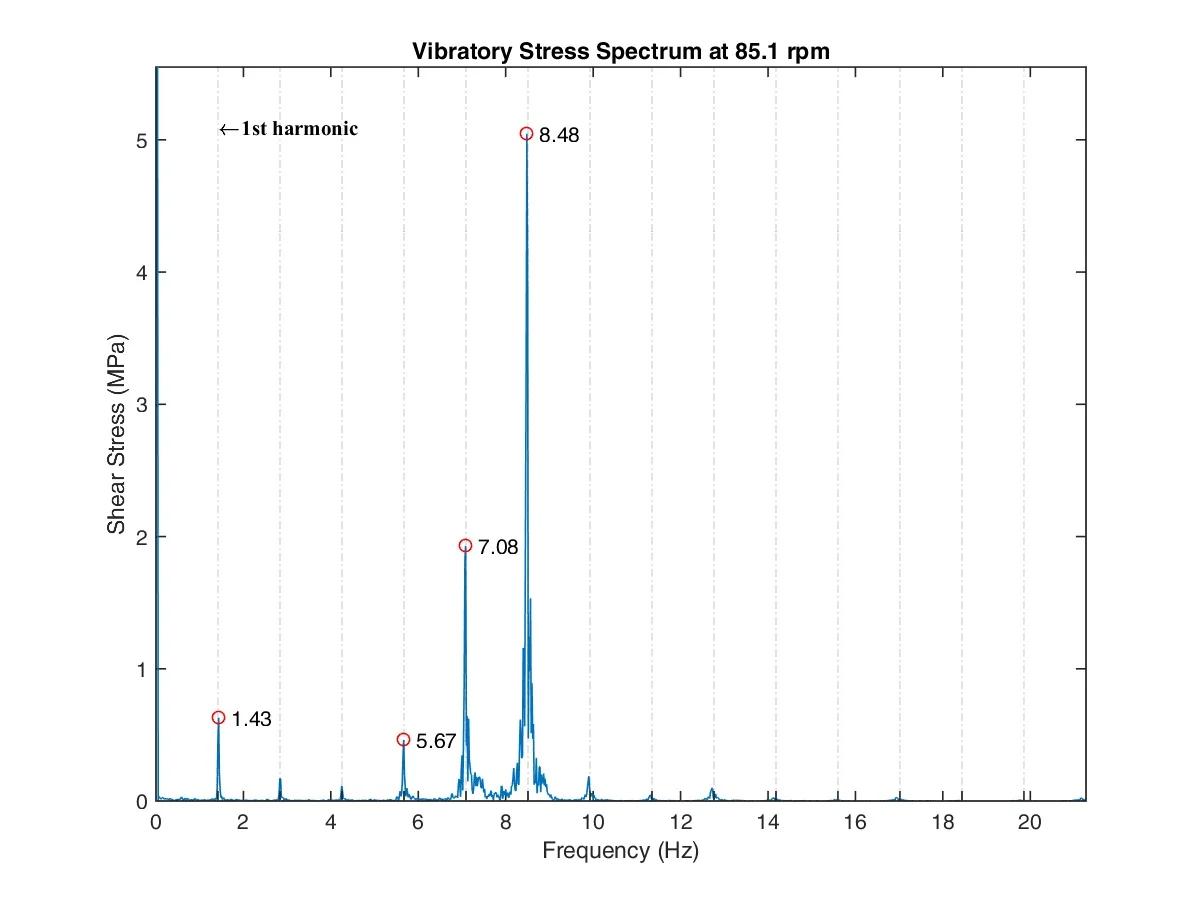

Propulsion torsional vibration measurements with the aid of the strain gauge technique