Two-stroke valve spindle and seat reconditioning possess a significant proportion of the reconditioned parts of marine engines. Valve spindles in particular are exposed to very high temperatures (>500°C at their centre) which combined with the presence of highly corrosive acids and low melting point salts can lead to high wear rates at the spindle bottom (~1mm/1000 hours in standard spindles). Furthermore, combustion by-products such as particulates can damage the contact areas of the spindle and seat resulting to loss of sealing and reduction in engine performance.
Up to now, standard type two-stroke exhaust valves (Stainless steel body, Cobalt based hardfacing alloy) have been routinely reconditioned using conventional techniques (GMAW/MIG is the most popular). However, the sophisticated materials of modern types (nickel based superalloys), require lower heat-inputs and extensive know-how. As a result only high-end surfacing techniques guarantee repeatable, metallurgically sound and cost efficient work. Laser Cladding with its low heat input characteristics and impeccable weld bead geometry control offers imperfection free overlays with operating costs which can be up to 70% lower compared to GMAW/MIG. The most important advantages of the technique are summarised below:
- Imperfection free overlays even with most demanding precipitation hardenable alloys
- Minimised machining allowances, reducing consumable and labour costs
- Less consumable costs. Thinner overlays possible with low dilution levels.
- Modern Laser Cladding systems have adequate deposition rates to combat competition from more conventional techniques
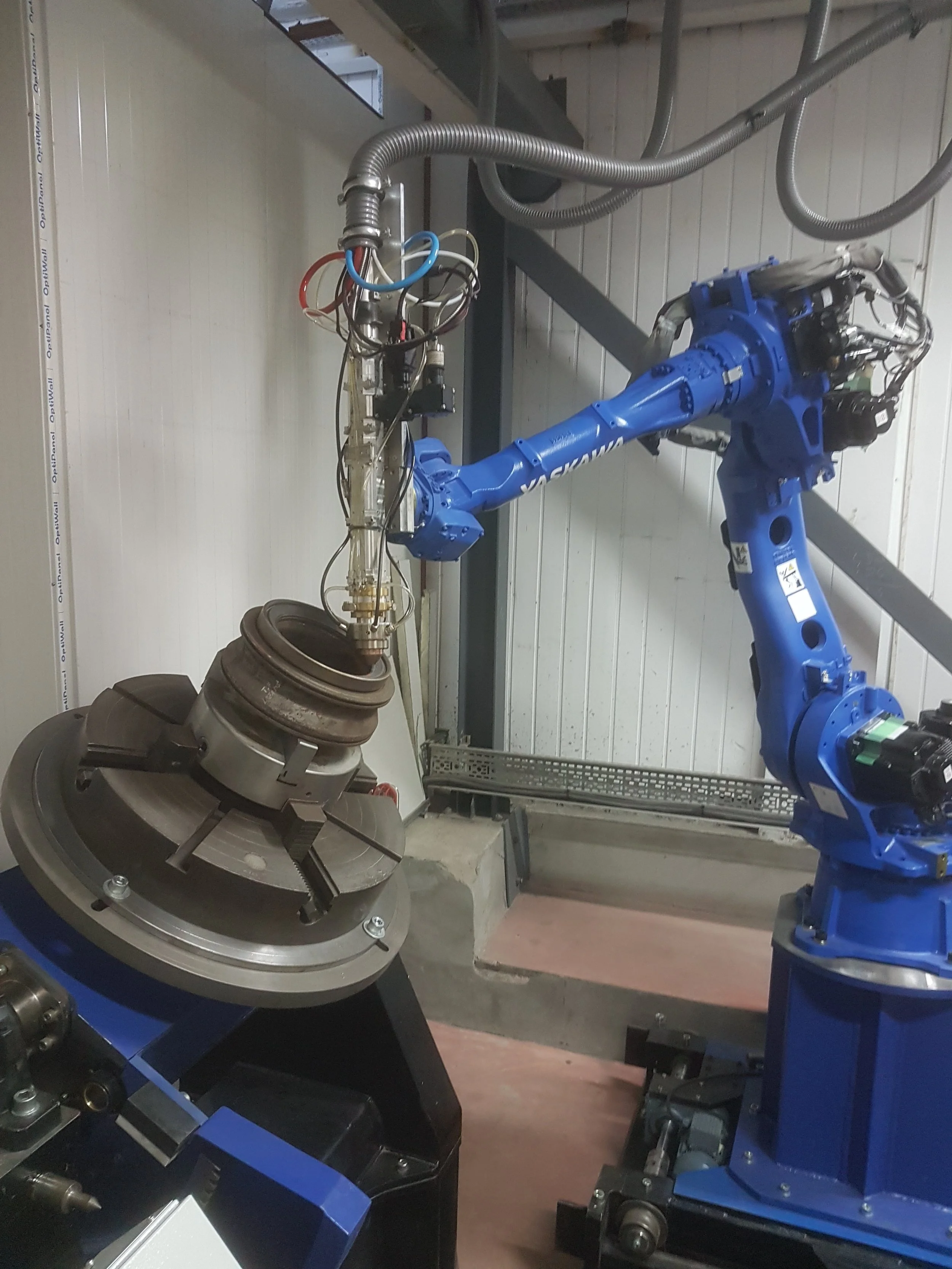