Cast iron is generally regarded as a material with poor weldability. Its high carbon content which is precipitated in the form of graphite flakes, nodules or spheroids results to the formation of hard martensitic phase in the heat affected zone during welding. This phase is often incapable of accommodating the thermal strains formed during cooling and results to cold cracking. Additionally, the relatively high content of phosphorous and sulphur often added to improve the fluidity of the melt, result to the formation of low temperature eutectics during the solidification of the weld metal. These eutectics in turn often lead to hot cracking effects.
Laser cladding with its localised and low heat input overcomes the above issues and renders weld overlaying of grey and malleable iron parts a routine. Additionally, the low levels of induced strains allow for the local repairs of castings with minimal distortions on neighbouring surfaces.
Four stroke pistons, cylinder covers and a range of small and large scale castings are routinely repaired using our systems and approved processes.
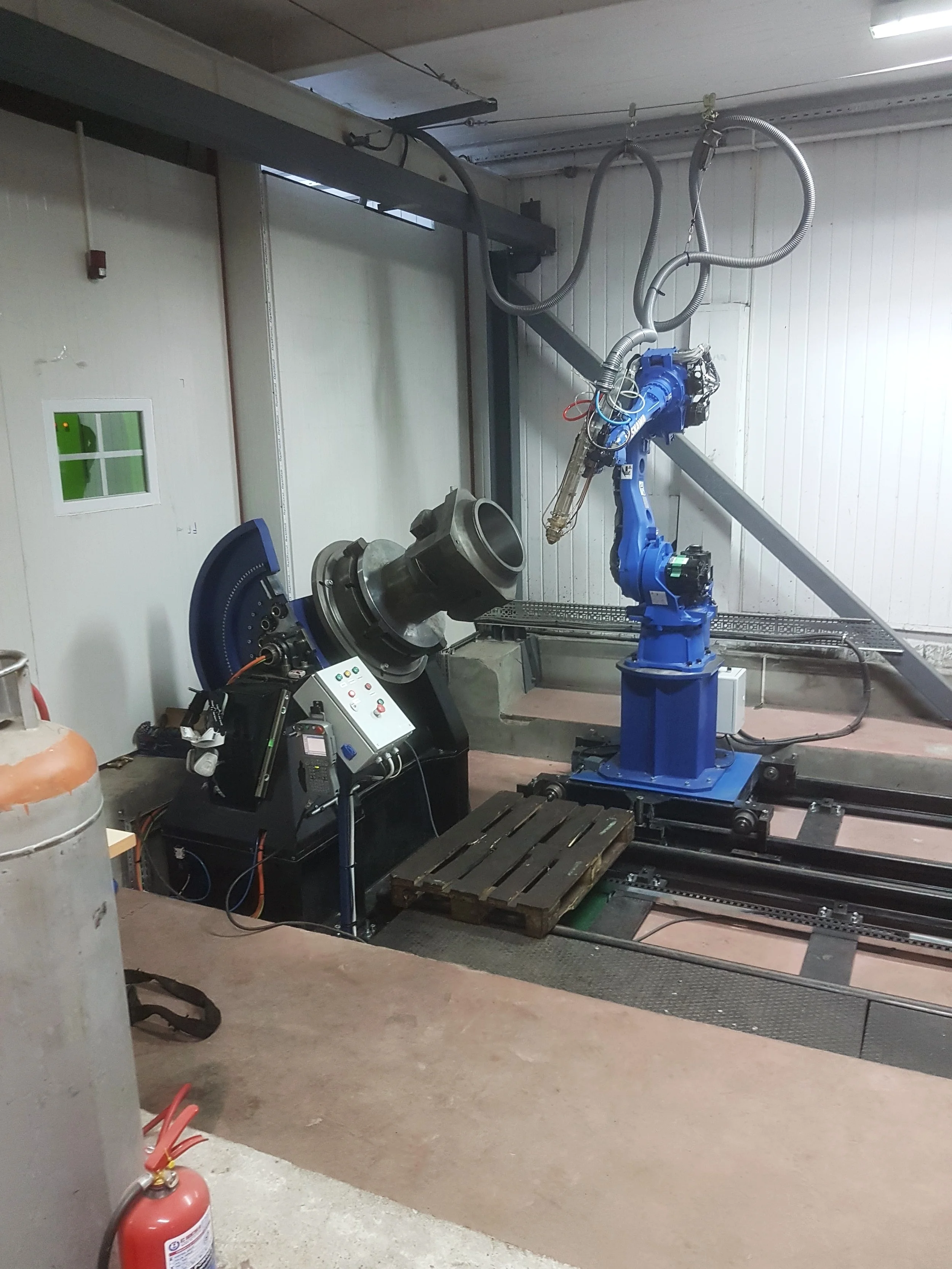



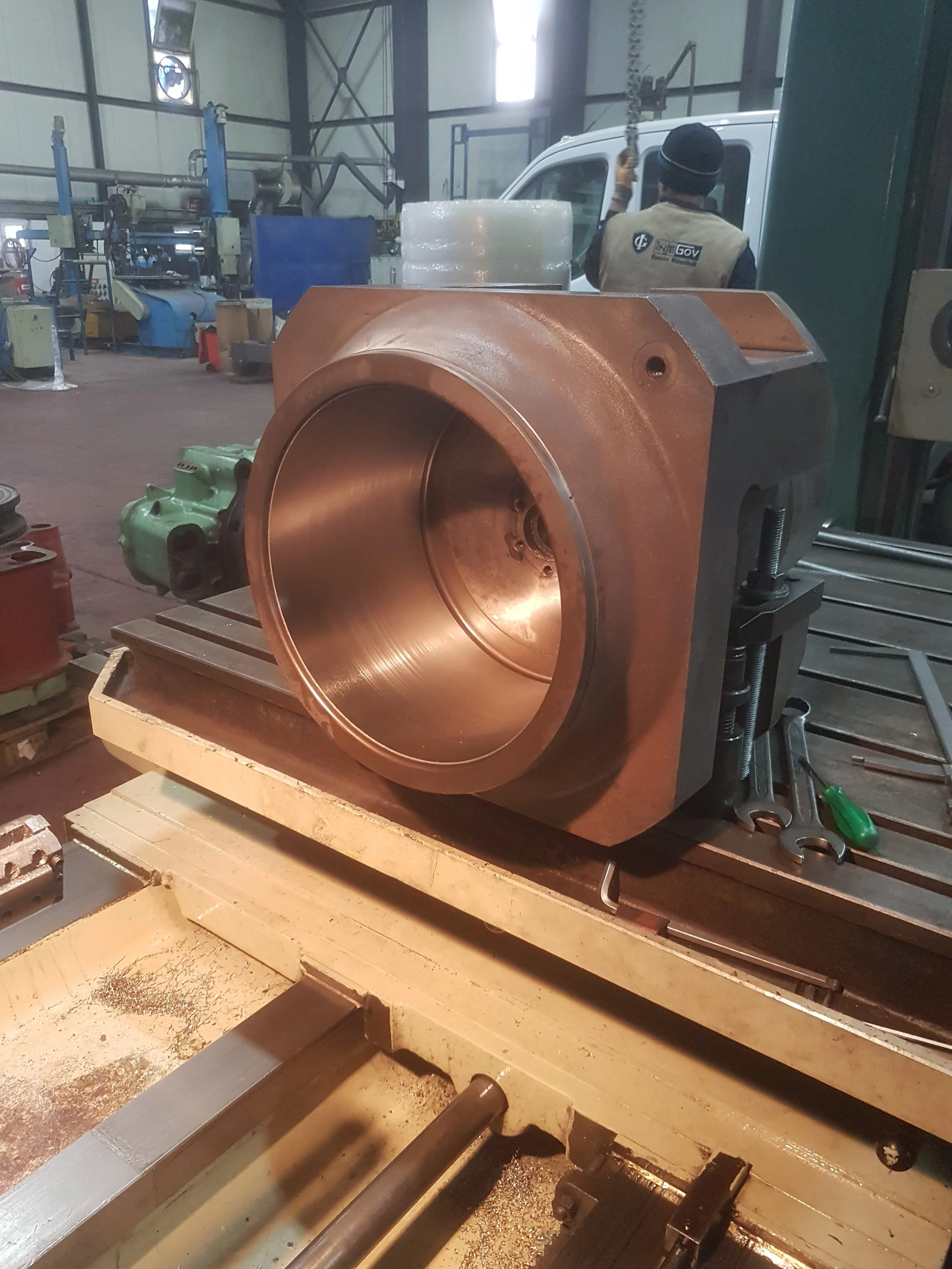




